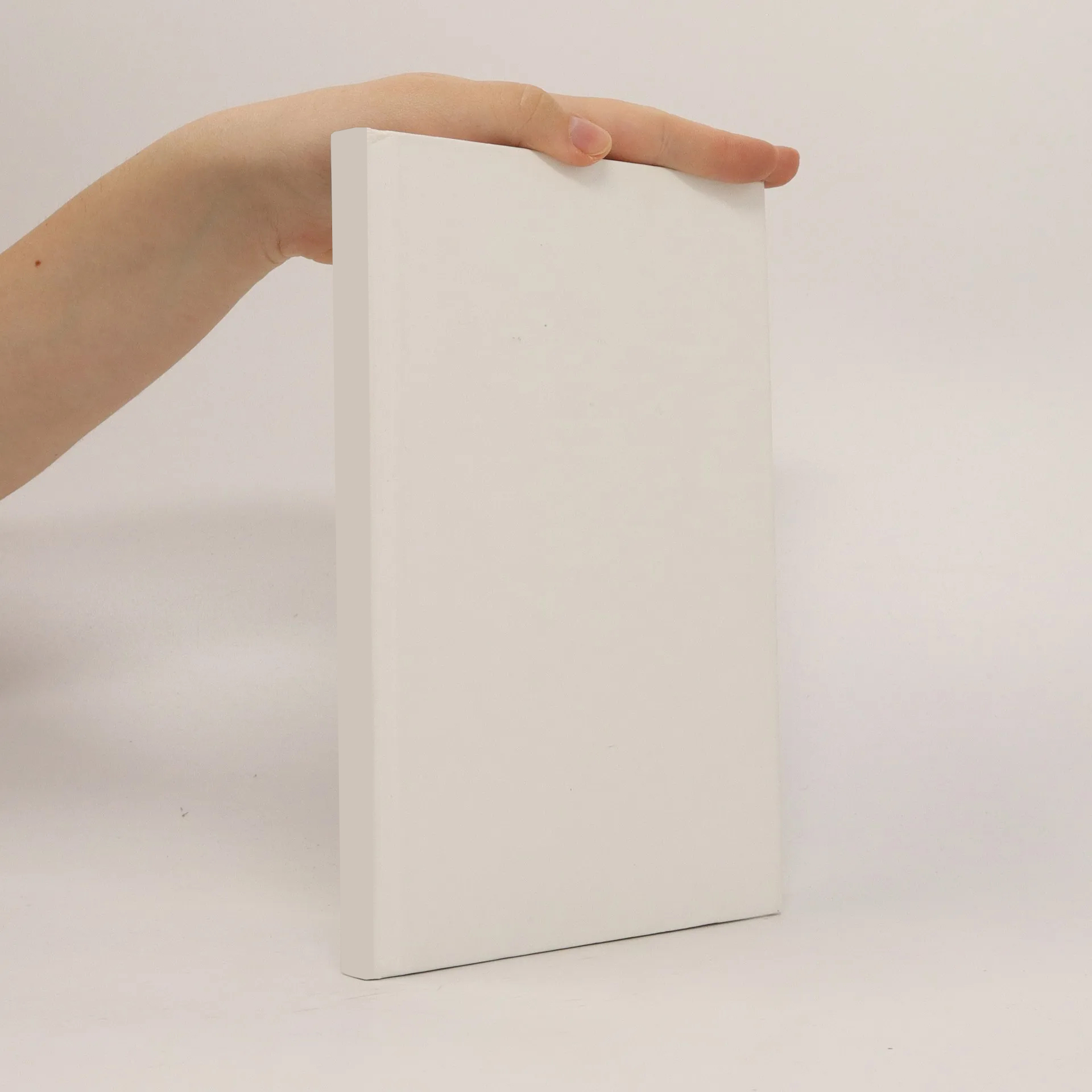
Více o knize
Staying competitive in the dynamic world of polymers requires constant optimization and innovation with special considerations given to reactors, as the type of the reactor and the condition under which the reaction is carried out are the key factors deciding the quality of the final polymer and thus, its application fields. Batch stirred tanks are the conventional choice in polymer production, even though this reactor configuration suffers from poor heat and mas transfer, high maintenance costs and lack of scalability. As a result, the emerging trend in the chemical industry emphasizes on replacing conventional reactors with smart-scaled tubular reactors operating in continuous mode, with the purpose of providing the fast and exothermic polymerization with a greater surface area to volume ratios and shorter diffusion paths. Despite all the benefits brought to the system by miniaturizing the reactor, the wall friction in addition to the increased viscosity in course of the polymerization, deviate the flow from ideal plug behaviour towards laminar regime, influencing the quality of the synthesised polymer negatively with increased chance of fouling. In an attempt to development a scalable reactor concept for polymer production, the impact of different flow patterns on fouling boundaries of the reactor as well as quality of the final polymer have been investigated in this work, on the example of free radical polymerization of Methyl methacrylate in solvent. Another considerable issue facing smart-scaled reactors is the development of suitable measurement methods to detect process parameters such as temperature. Fibre Brag Grating Sensor has been utilized as a less invasive temperature measurement tool that enables thermal analysis on the reacting system.
Nákup knihy
Scalability of milli-structured reactors for continuous polymerization, Nazanin Entesari
- Jazyk
- Rok vydání
- 2015
Doručení
Platební metody
Nikdo zatím neohodnotil.