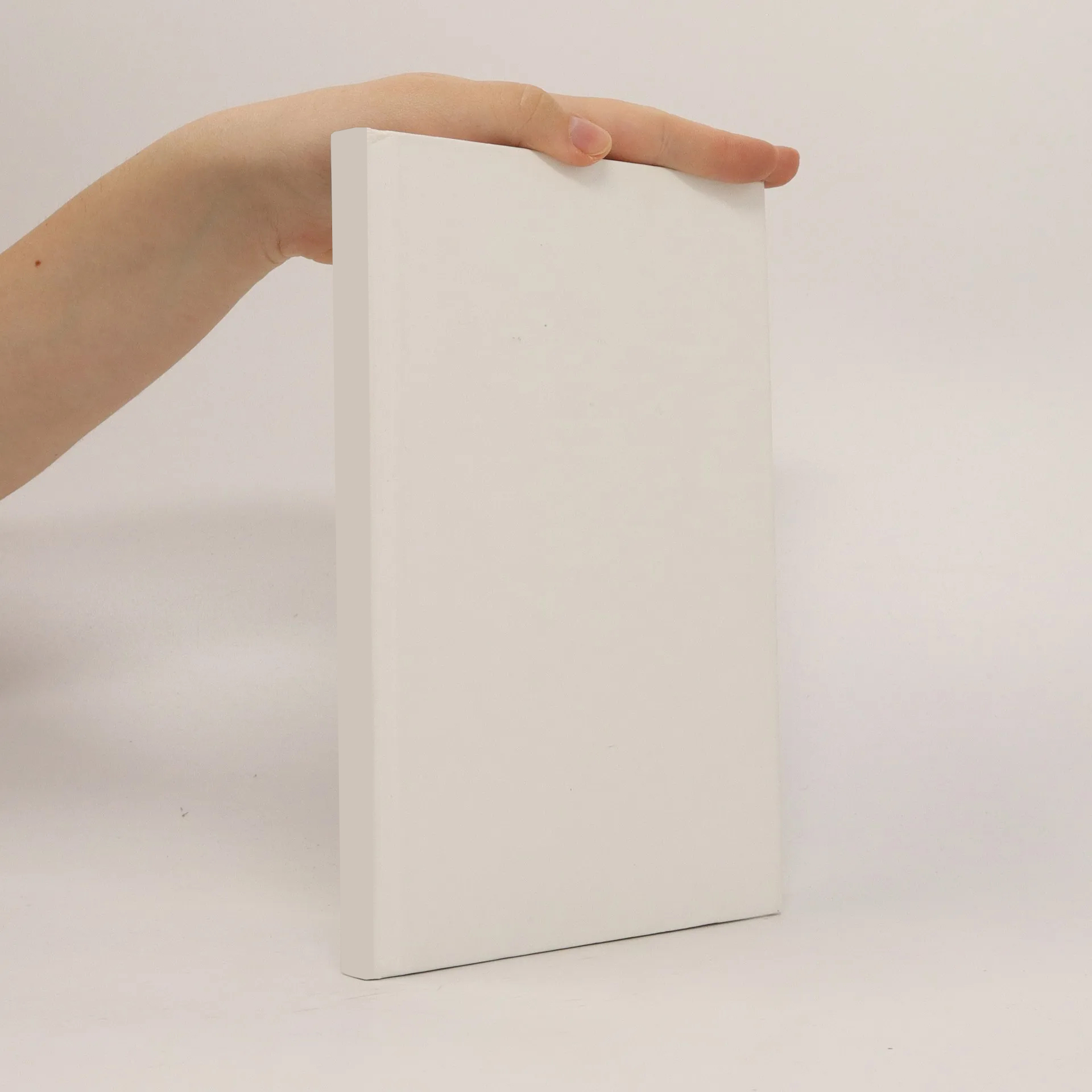
Více o knize
The conventional sheet metal forming processes need part dependent tooling, which costs in terms of time and money. Due to these factors along with increasing variants variety in the sheet metal part fabrication, highly flexible forming processes are being developed. The Incremental Sheet Metal Forming (ISMF) is one of the emerging flexible forming technologies in the sheet metal engineering, which rather uses universal tooling that is mostly part independent. Hence, the process offers higher flexibility reducing the product development time greatly, and making it very suitable for low volume production. Fundamentally, a desired shape is formed on a fixed form defining support tool using an active small size-forming tool in the ISMF process. The aim of the presented dissertation is to realize the ISMF with different flexible supporting strategies compared to the form defining support strategies in order to acquire some basic information for building a machine for an advanced flexible forming process called as the Kinematical Incremental Sheet Metal Forming (KISMF). The tool path is one of the main process controlling variables and hence, different tool paths were studied to know the unique strengths of each tool path. Thereafter, several experiments were conducted using a CNC milling machine and a generalpurpose CAD/CAM system to avail the benefits, which are often confined to a special machine and software. The main objectives were the optimization of the process variables, including the tool path optimizations in order to form higher quality parts with minimum tooling and experiments. The experiments conducted from simple to complex shape categories revealed different suitable process controlling variables and tool paths. Further, different techniques to attain competitive part quality using simple flexible supports are reported. The competitive part quality is also governed by the thickness distribution that is dependent on the apex angle. Therefore, the optimum offset essential to overcome the limitations of forming with the sine law as per the apex angle and associated thinning are proved by forming a complex shape with almost vertical walls. Subsequently, an appropriate approach using preformed sheets was explored during the research to minimize thinning at lower apex angles. Based on the ISMF research results, some basic ideas for the realization of the KISMF process are presented. Finally, the conclusions of the contributed work have directed the research on the key potential areas, including the KISMF. The scope of this work summarizes the directions for production of parts with simple flexible tooling for expanding the process competence spectrum.
Nákup knihy
Basic investigations of the incremental sheet metal forming process on a CNC milling machine, Sanjay Jadhav
- Jazyk
- Rok vydání
- 2005
- product-detail.submit-box.info.binding
- (měkká)
Doručení
Platební metody
Nikdo zatím neohodnotil.