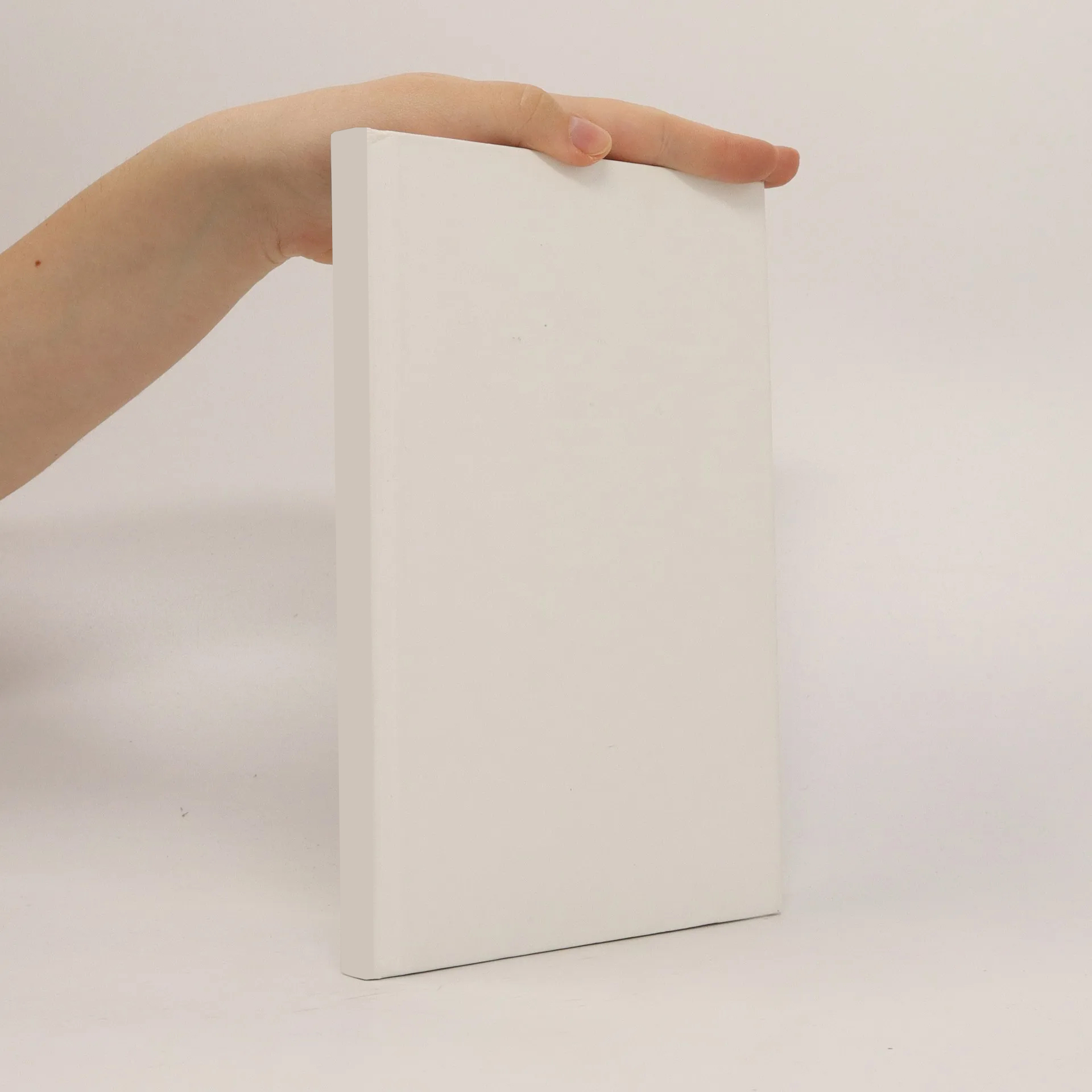
Více o knize
In this thesis, focus is drawn to the modelling of the mechanical behaviour of two types of products that feature increased functionality. To this end, the finite element method (FEM) is utilized and enhancements of the FEM are presented which enable an improved modelling in order to simulate the mechanical behaviour of the two products of interest. In the first application, a new hybrid production process regarding the production of large ring-shaped devices that feature a wear-resistant outer layer is proposed. The layer itself is produced from powdery metal matrix composite (MMC) and is applied onto a substrate ring. In the novel production process, ring rolling and compaction of the layer are combined into one production step. Thereby, current limitations like the maximal producible ring size can be exceeded. For an adequate modelling of the process, a material model is derived that is able to describe the compaction of metal powders. Finally, the material model is applied within longitudinal and ring rolling simulations of a powder-filled bar and ring, respectively. The second example of a product with increased functionality is concerned with stents made out of nickel-titanium alloys (Nitinol). Due to the filigree structures of stents, appropriate finite element models feature a large number of degrees of freedom resulting in very long computing times. As a remedy, we present a novel finite element technology which we call solid-beam element. The performance of the element is assessed using various benchmark problems from literature. Finally, the proposed finite element technology is successfully applied to the modelling of stent structures including a complete intracranial stent.
Nákup knihy
New finite element modelling techniques for functional materials and devices, Jan Frischkorn
- Jazyk
- Rok vydání
- 2019
Doručení
Platební metody
Nikdo zatím neohodnotil.