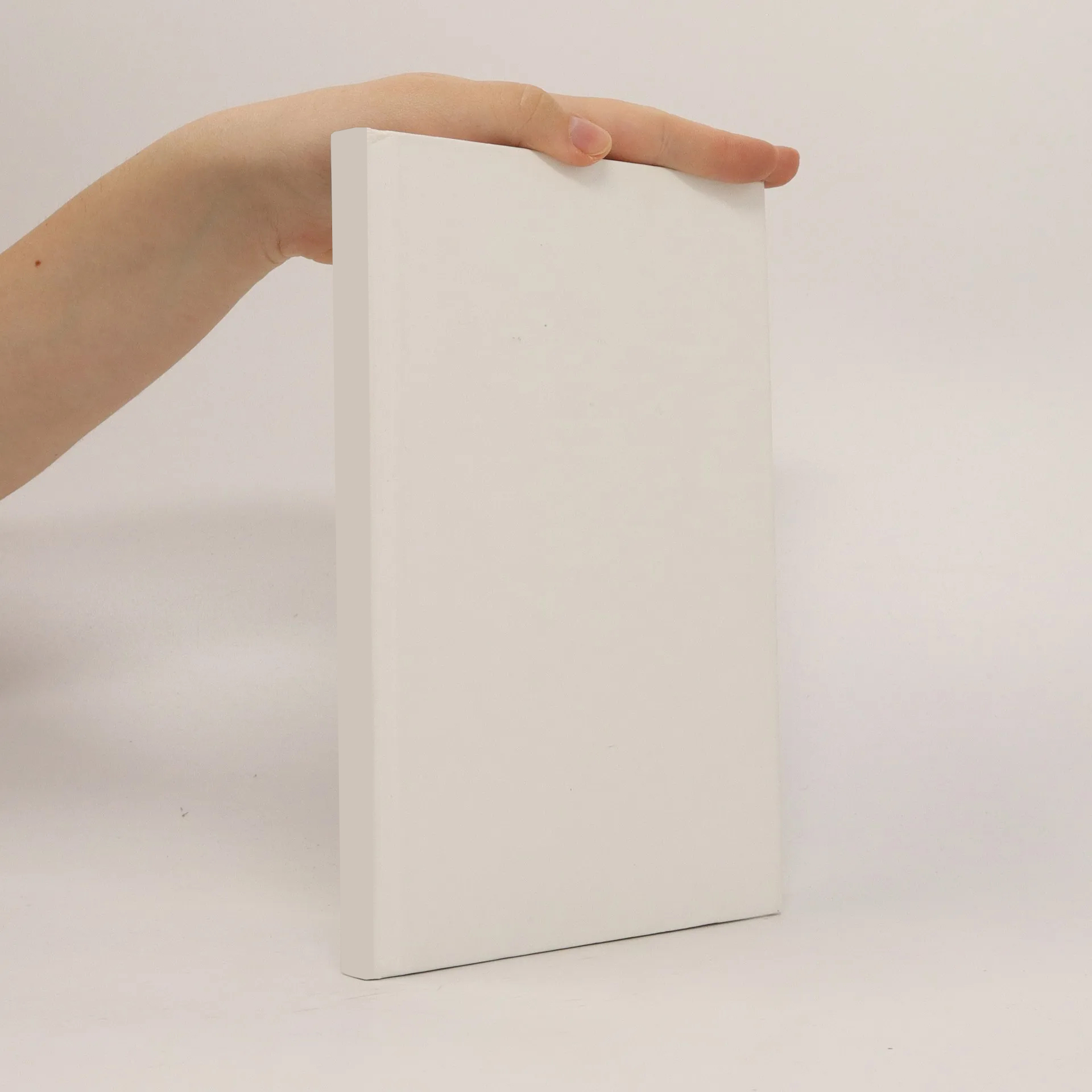
Simulations of roll forming processes on the basis of steady state properties
Autoři
Parametry
Více o knize
The application of a numerical analysis such as the finite element method to investigate a roll forming process allows for a precise analysis of the process state variables. By studying the process parameters, the effects of these numerous factors on the final results can be determined. The main obstacle for the economic use of the FEM as a process design method is the high computational time, which reaches several days or weeks. A lot of researches have been conducted to develop new analytical and numerical methods to determine the longitudinal strain at the band edge. These methods have offered time-saving alternatives only for the studied profile shape, therefore they do not allow for a comprehensive consideration. Above all, it is not possible through them to identify individual process state variables, which significantly influence the final geometry. Furthermore, by using these methods to accelerate the simulation of a roll forming process, the quality of the results changes for the worse. None of the available methods explicitly takes into account the steady state conditions of the roll forming process. In this study, the aim of the presented work was the use of the steady state behaviour to accelerate the FE-simulation. The steady state behaviour in a roll forming process was investigated and confirmed in this work. On the basis of it, a new numerical algorithm (Steady State Extrapolation Algorithm SSEA) was developed, which takes advantages of the steady state properties in the roll forming process. For applying the developed algorithm, a numerical simulation is started and proceeded until the steady state zone appears. The identification of the steady state zone occurs through the mentioned criteria in this study. As soon as these criteria are satisfied, the simulation is stopped and the SSEA is started. The SSEA computes the new state variables for the next time steps in the actual forming step. At the same time, the sheet metal is translated to the end of this forming step i. e. to the next contact zone. A new output file is generated and used as an input file for the numerical simulation of the next forming step. Afterwards, the numerical simulation is continued to compute the kinematic behaviour of the sheet metal for the next forming step. The above mentioned sequence is repeated until the simulation is finished. The evaluations of the longitudinal plastic strain at the band edge and the comparison between the results computed with and without the SSEA have shown, that the quality of the results computed using the SSEA is about the same as in the conventional simulation. The average deviation ranges between 5% and 10% and is caused by minor inaccuracies in the extrapolation of the displacements and the state variables. Its influence on the process design is considered to be low. Furthermore, the final bending angles computed with and without the SSEA were investigated. The results have depicted, that the simulation with the SSEA generates the same final bending angle as the simulation without the SSEA. Furthermore, the computational time required for the execution of the SSEA was reduced, and so it can be neglected. Overall, the use of the steady state properties by applying the SSEA with regard to the investigated profiles reduces the necessary computational time by at least 45%.
Nákup knihy
Simulations of roll forming processes on the basis of steady state properties, Ahmad Abrass
- Jazyk
- Rok vydání
- 2014
Doručení
Platební metody
2021 2022 2023
Navrhnout úpravu
- Titul
- Simulations of roll forming processes on the basis of steady state properties
- Jazyk
- anglicky
- Autoři
- Ahmad Abrass
- Vydavatel
- Shaker
- Rok vydání
- 2014
- ISBN10
- 3844028862
- ISBN13
- 9783844028867
- Série
- Berichte aus Produktion und Umformtechnik
- Kategorie
- Skripta a vysokoškolské učebnice
- Anotace
- The application of a numerical analysis such as the finite element method to investigate a roll forming process allows for a precise analysis of the process state variables. By studying the process parameters, the effects of these numerous factors on the final results can be determined. The main obstacle for the economic use of the FEM as a process design method is the high computational time, which reaches several days or weeks. A lot of researches have been conducted to develop new analytical and numerical methods to determine the longitudinal strain at the band edge. These methods have offered time-saving alternatives only for the studied profile shape, therefore they do not allow for a comprehensive consideration. Above all, it is not possible through them to identify individual process state variables, which significantly influence the final geometry. Furthermore, by using these methods to accelerate the simulation of a roll forming process, the quality of the results changes for the worse. None of the available methods explicitly takes into account the steady state conditions of the roll forming process. In this study, the aim of the presented work was the use of the steady state behaviour to accelerate the FE-simulation. The steady state behaviour in a roll forming process was investigated and confirmed in this work. On the basis of it, a new numerical algorithm (Steady State Extrapolation Algorithm SSEA) was developed, which takes advantages of the steady state properties in the roll forming process. For applying the developed algorithm, a numerical simulation is started and proceeded until the steady state zone appears. The identification of the steady state zone occurs through the mentioned criteria in this study. As soon as these criteria are satisfied, the simulation is stopped and the SSEA is started. The SSEA computes the new state variables for the next time steps in the actual forming step. At the same time, the sheet metal is translated to the end of this forming step i. e. to the next contact zone. A new output file is generated and used as an input file for the numerical simulation of the next forming step. Afterwards, the numerical simulation is continued to compute the kinematic behaviour of the sheet metal for the next forming step. The above mentioned sequence is repeated until the simulation is finished. The evaluations of the longitudinal plastic strain at the band edge and the comparison between the results computed with and without the SSEA have shown, that the quality of the results computed using the SSEA is about the same as in the conventional simulation. The average deviation ranges between 5% and 10% and is caused by minor inaccuracies in the extrapolation of the displacements and the state variables. Its influence on the process design is considered to be low. Furthermore, the final bending angles computed with and without the SSEA were investigated. The results have depicted, that the simulation with the SSEA generates the same final bending angle as the simulation without the SSEA. Furthermore, the computational time required for the execution of the SSEA was reduced, and so it can be neglected. Overall, the use of the steady state properties by applying the SSEA with regard to the investigated profiles reduces the necessary computational time by at least 45%.