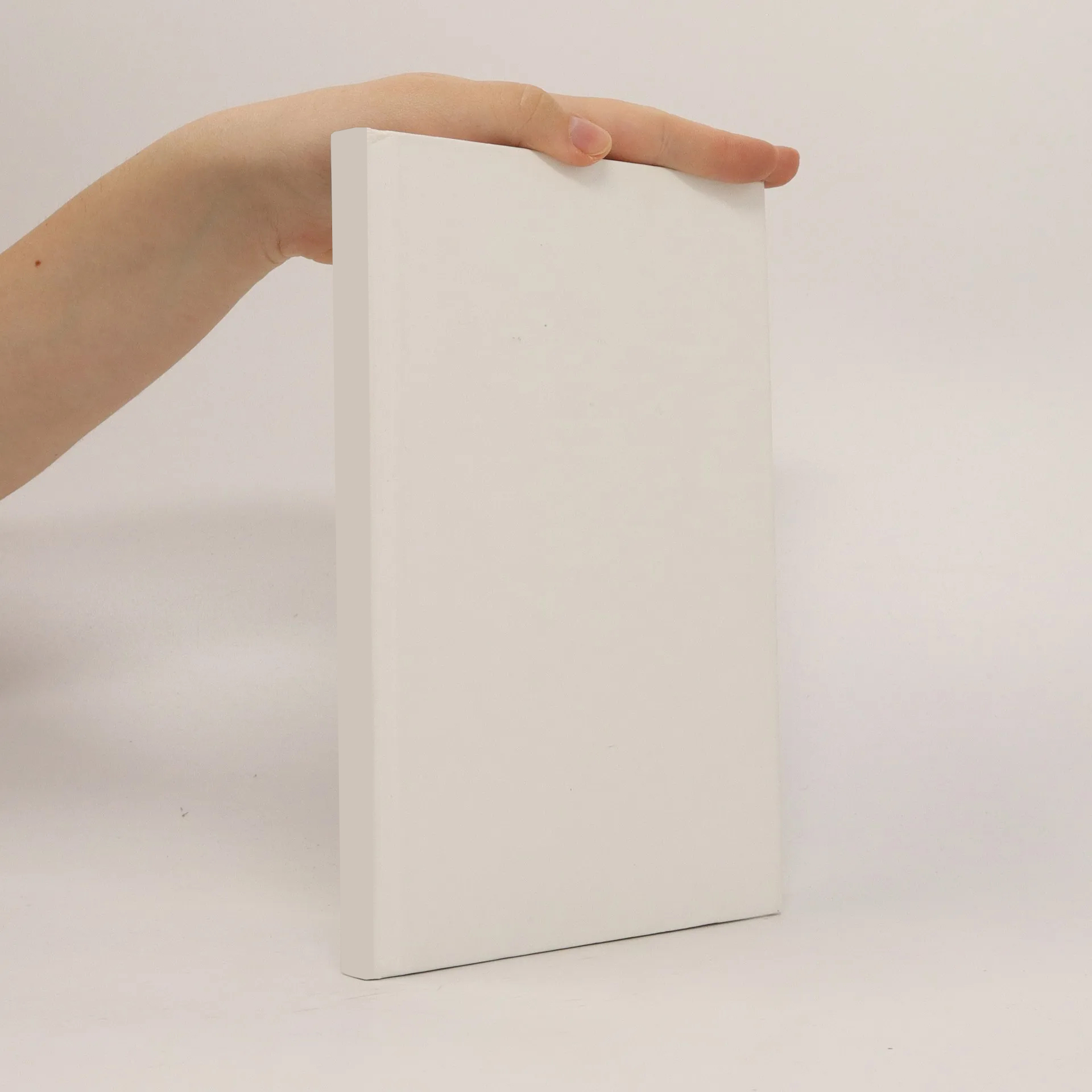
Microstructure evolution during thermomechanical multi-step processing of extruded aluminum profiles
Autoři
Parametry
Více o knize
In order to meet the demands of specific mechanical properties and to introduce additional functional elements in the geometry of the extruded profiles, subsequent forming processes are required. Utilization of electromagnetic forming subsequent to hot aluminum extrusion to manufacture functionally graded extrusion profiles is an innovative forming technology. The large deformations, intermediate to very extreme strain rates and elevated temperatures, which characterize the process chain of hot extrusion and subsequent electromagnetic compression, lead to a complex development in the microstructure which is linked to the mechanical properties of the material. The evolution of the microstructure during thermomechanical multi-step processing of extruded aluminum profiles has not been investigated explicitly. The main aim of this research was to investigate the effect of thermomechanical processing conditions on the microstructure evolution for a wide range of plastic strain rates. First, the microstructural evolution during the hot direct extrusion of EN AW-6082 was investigated. A novel experimental approach was introduced, which preserves the dynamic evolution of grains by avoiding secondary recrystallization. Here, the dynamic grain structure evolution of a single material point was characterized by monitoring its migration along the flow line during extrusion. The resulting microstructure was related to the deformation history. The effects of very high strain rates and temperatures on microstructural evolution under impulse loading conditions were analyzed and modelled as well. In order to predict the final microstructure of the thermomechanically processed material, the entire process chain was simulated based on the proposed dynamic recrystallization model.
Nákup knihy
Microstructure evolution during thermomechanical multi-step processing of extruded aluminum profiles, Ahmet Güzel
- Jazyk
- Rok vydání
- 2015
Doručení
Platební metody
2021 2022 2023
Navrhnout úpravu
- Titul
- Microstructure evolution during thermomechanical multi-step processing of extruded aluminum profiles
- Jazyk
- anglicky
- Autoři
- Ahmet Güzel
- Vydavatel
- Shaker
- Rok vydání
- 2015
- ISBN10
- 3844034285
- ISBN13
- 9783844034288
- Série
- Reihe Dortmunder Umformtechnik
- Kategorie
- Skripta a vysokoškolské učebnice
- Anotace
- In order to meet the demands of specific mechanical properties and to introduce additional functional elements in the geometry of the extruded profiles, subsequent forming processes are required. Utilization of electromagnetic forming subsequent to hot aluminum extrusion to manufacture functionally graded extrusion profiles is an innovative forming technology. The large deformations, intermediate to very extreme strain rates and elevated temperatures, which characterize the process chain of hot extrusion and subsequent electromagnetic compression, lead to a complex development in the microstructure which is linked to the mechanical properties of the material. The evolution of the microstructure during thermomechanical multi-step processing of extruded aluminum profiles has not been investigated explicitly. The main aim of this research was to investigate the effect of thermomechanical processing conditions on the microstructure evolution for a wide range of plastic strain rates. First, the microstructural evolution during the hot direct extrusion of EN AW-6082 was investigated. A novel experimental approach was introduced, which preserves the dynamic evolution of grains by avoiding secondary recrystallization. Here, the dynamic grain structure evolution of a single material point was characterized by monitoring its migration along the flow line during extrusion. The resulting microstructure was related to the deformation history. The effects of very high strain rates and temperatures on microstructural evolution under impulse loading conditions were analyzed and modelled as well. In order to predict the final microstructure of the thermomechanically processed material, the entire process chain was simulated based on the proposed dynamic recrystallization model.