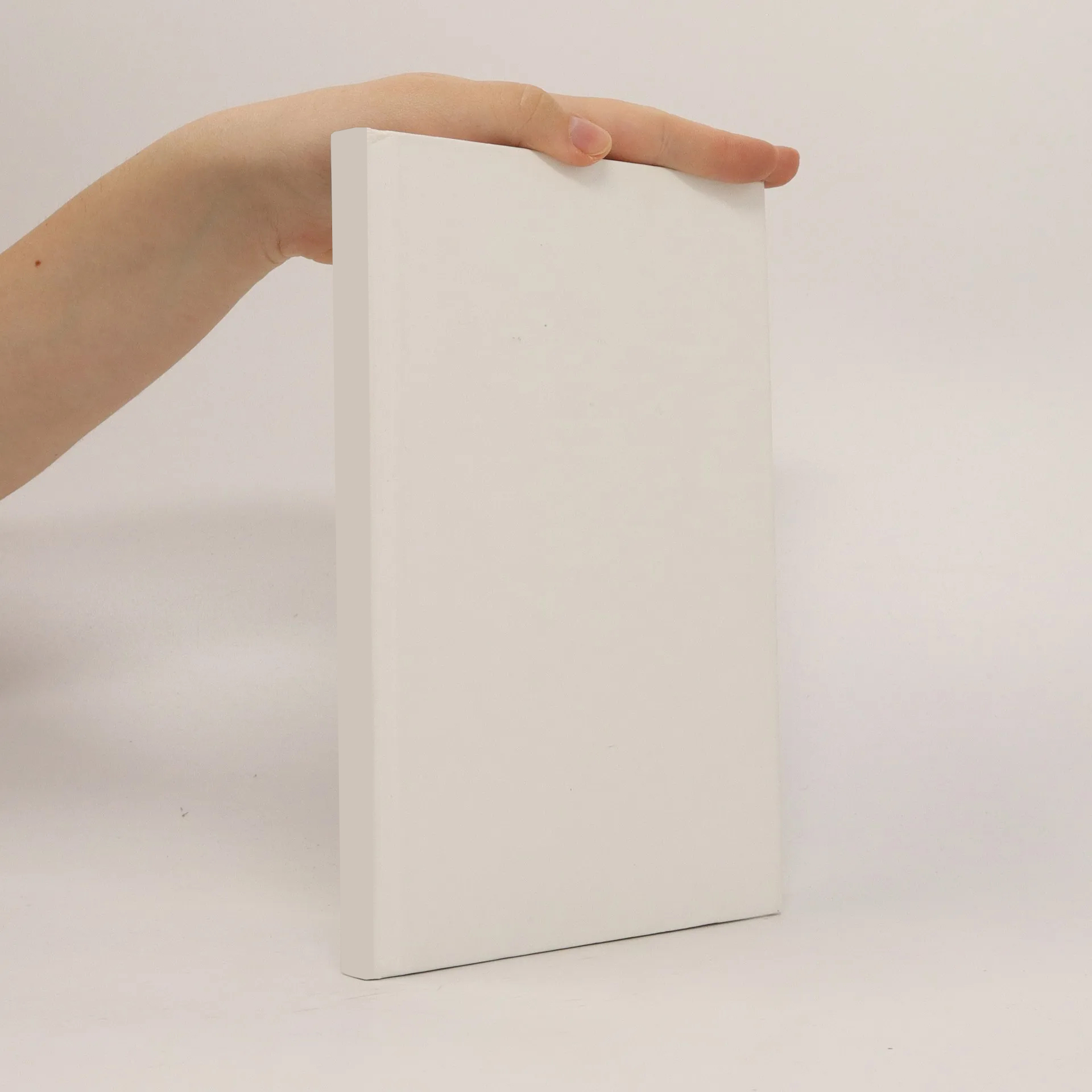
Thermodynamic and one-dimensional kinetic simulations applied to material interfaces produced via powder metallurgy processes
Autoři
Více o knize
The joining of different materials into one part is an advantageous method to combine different properties in high technology components designed for special applications. For the production of these parts, various methods can be applied, for example the powder metallurgy. Powders can be sintered together or onto dense surfaces, thus combining materials with different chemical compositions. Due to their chemical potential and atomic mobilities, they form interfaces, which phases can precipitate and influence on the desired properties of the component. In order to avoid the formation of any unfavourable phase which could decrease the performance of the part, the weld-line is the target of intensive research and numerous experiments and analyses. In this work, a simulation-based approach is introduced and evaluated as an alternative to actual experiments in order to predict the behaviour of this zone. A commercial one-dimensional kinetic software Thermo-Calc I DICTRA, based on the CALPHAD method, for the analysis of bulk materials is being used for predictions of sintered interfaces. Since the assumed conditions of the software are not the same of the analytical conditions - Le. only diffusion-controlled mechanisms are taken into account, dense materials, absence of grain boundaries, diffusion only in one dimension, equilibrium content of vacancies - experimental and simulated results are compared. The applicability of the software is tested using two powder metallurgic processes: Two-Component Metal Injection Moulding (2C-MIM) and stencil printing with powder-filled pastes. For the 2C-MIM parts, three material combinations (FeNi 7wt% with FeNi 50wt%, 316L with 17-4PH, and 316L with M2) are examined. Energy dispersive X-ray I scanning electron microscopy line scans across the interfaces, metallography visualization and quantification of the phases are compared to the simulated interdiffusion profiles, the phases' distribution across the interfaces and phase diagrams respectively. For the experiments, powders with different particle sizes and manufacturing techniques, e. g. pre-alloyed and elemental powders, are sintered at different temperatures and for different durations. Comparisons between experiments and simulation show consistent agreement. The largest normalized average error (discrepancy) between simulated and experimental interdiffusion profiles is approximately 10 % for the element nickel in the 316L and 17-4PH interface. Different powder particle sizes and manufacturing techniques did not influence the formation of the interface significantly. For stencil printed parts, one material combination is processed (FeCrNi printed onto 316L sheet material). For stencil printed parts, interdiffusion profiles are also measured and simulated, so that the error value reaches approximately 23 % for nickel. The discrepancies between simulation and experiments are attributed to the pores in the coating zone which interfere with the common solid-state diffusion directions. The limitations of the software for application in sintered interface are described, Le. minimum porosity, homogeneous microstructures and flat interface are required. Nevertheless, the comparisons reveal that DICTRA and Thermo-Calc are valuable tools to describe the interdiffusion in powder metallurgical produced interfaces.