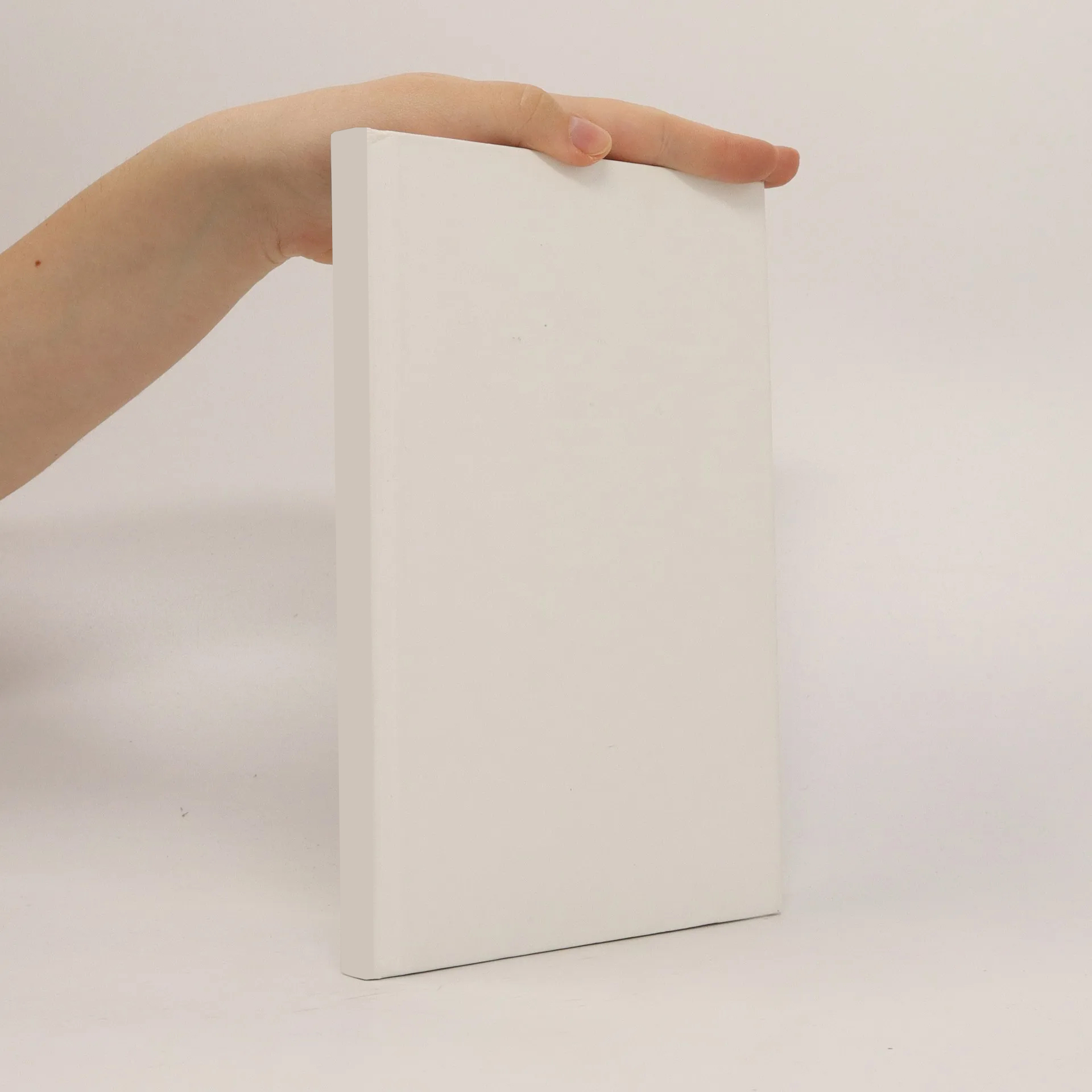
Optimization and coupling strategies for codes of different fidelity to automate an aerodynamic compressor design process
Autoři
Parametry
Více o knize
The aerodynamic compressor design process design process generally consists of four phases in which tools with increasing fidelity are applied to design step by step a complete compressor from mere performance data. The process starts with a 1D Meanline code where the annulus geometry and flow values along the midline are defined. Secondly, a Throughflow code is applied to define streamlines. A subsequent blading process determines the actual blade shape. Finally, a 3D CFD code is typically employed to validate the designed compressor. In the underlying thesis, these four tools are used within automated workflows in order to conduct the aerodynamic compressor design process in an automated manner. For each design phase optimization problems are outlined and investigated. This work specifically focuses on the development of coupling strategies for the participating design codes and phases. At each design step of the process, the automated workflows are used to solve multi-objective optimization problems. Since the result of such an optimization problem is not a single design but a Pareto-front consisting of several designs, the challenging question arises of how to transfer complete Pareto-fronts from one design phase to the next. The answer leads to a sequence of new problems which are solved with a newly developed alternative problem formulation called COA. The thesis discusses the development of this approach in detail. The design transfer within the aerodynamic compressor design process is tackled with COA and demonstrates the advantages of this new approach. Finally, several created compressor configurations are compared using 3D CFD analysis. From this last assessment recommendations concerning the role and importance of the different design codes are drawn.
Nákup knihy
Optimization and coupling strategies for codes of different fidelity to automate an aerodynamic compressor design process, Fiete Pöhlmann
- Jazyk
- Rok vydání
- 2015
Doručení
Platební metody
Navrhnout úpravu
- Titul
- Optimization and coupling strategies for codes of different fidelity to automate an aerodynamic compressor design process
- Jazyk
- anglicky
- Autoři
- Fiete Pöhlmann
- Vydavatel
- Shaker Verlag
- Rok vydání
- 2015
- ISBN10
- 3844040293
- ISBN13
- 9783844040296
- Kategorie
- Skripta a vysokoškolské učebnice
- Anotace
- The aerodynamic compressor design process design process generally consists of four phases in which tools with increasing fidelity are applied to design step by step a complete compressor from mere performance data. The process starts with a 1D Meanline code where the annulus geometry and flow values along the midline are defined. Secondly, a Throughflow code is applied to define streamlines. A subsequent blading process determines the actual blade shape. Finally, a 3D CFD code is typically employed to validate the designed compressor. In the underlying thesis, these four tools are used within automated workflows in order to conduct the aerodynamic compressor design process in an automated manner. For each design phase optimization problems are outlined and investigated. This work specifically focuses on the development of coupling strategies for the participating design codes and phases. At each design step of the process, the automated workflows are used to solve multi-objective optimization problems. Since the result of such an optimization problem is not a single design but a Pareto-front consisting of several designs, the challenging question arises of how to transfer complete Pareto-fronts from one design phase to the next. The answer leads to a sequence of new problems which are solved with a newly developed alternative problem formulation called COA. The thesis discusses the development of this approach in detail. The design transfer within the aerodynamic compressor design process is tackled with COA and demonstrates the advantages of this new approach. Finally, several created compressor configurations are compared using 3D CFD analysis. From this last assessment recommendations concerning the role and importance of the different design codes are drawn.