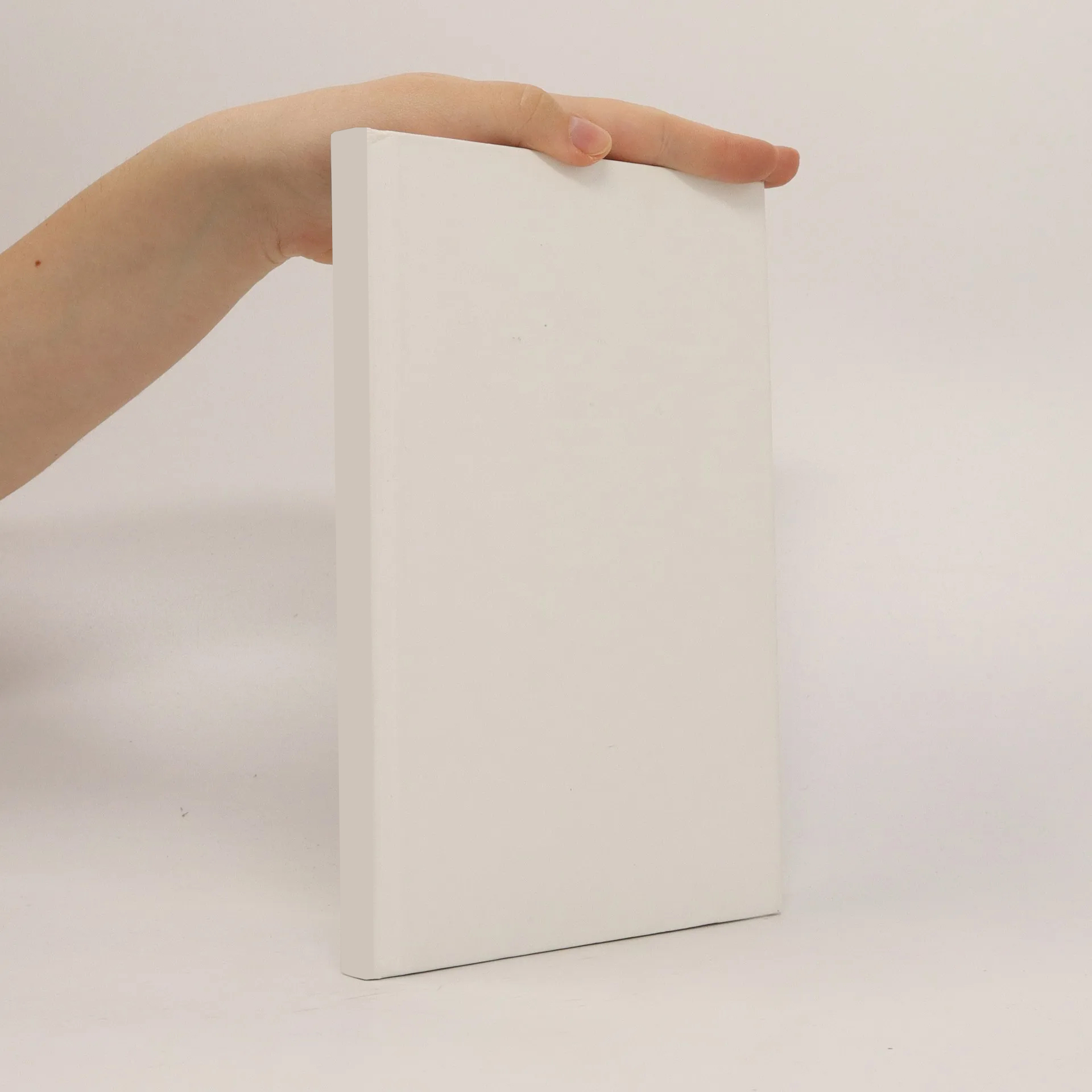
Hochtemperaturaktive HPPMS-Verschleißschutzschichten durch Bildung reibmindernder Magnéli-Phasen im System (Cr,Al,X)N
Autoři
Více o knize
The innovative hot stamping process press hardening offers the potential to produce high-strength and complex structural components for the automotive industry. However, the combination of mechanical and thermal loads in press hardening process places high demands on the tool surface. In addition to the metal forming the cutting processes are also of great importance in the production of structural and functional components. The most rapidly fast growing material group in this sector are the difficult to machine materials such as titanium alloys and hard steels. Unfavorable factors in the processing of these materials are their high strength, their low thermal conductivity and their tendency to work hardening. Nowadays, wear resistant coatings deposited via physical vapour deposition (PVD) and chemical vapour deposition (CVD) have been used in order to extend the lifetime of cutting and forming tools. But the progressive use of difficult to machine materials places high demands on the coatings. The present work deals with the synthesis and characterization of PVD hard coatings for high temperature tool applications. The focus is on the development of chrome based coatings using the novel high power pulsed magnetron sputtering (HPPMS) technology. For this reason, a (Cr, Al)N hard matrix is modified with different alloying elements that form so-called Magnéli phases. Afterwards, the high temperature behaviour of the coatings is investigated by annealing test in atmosphere. The investigation of the tribological behaviour is carried out using a high temperature tribometer. Finally, coated tools are tested in press hardening and turning experiments in order to evaluate their performance and feasibility for hot forming and cutting applications.