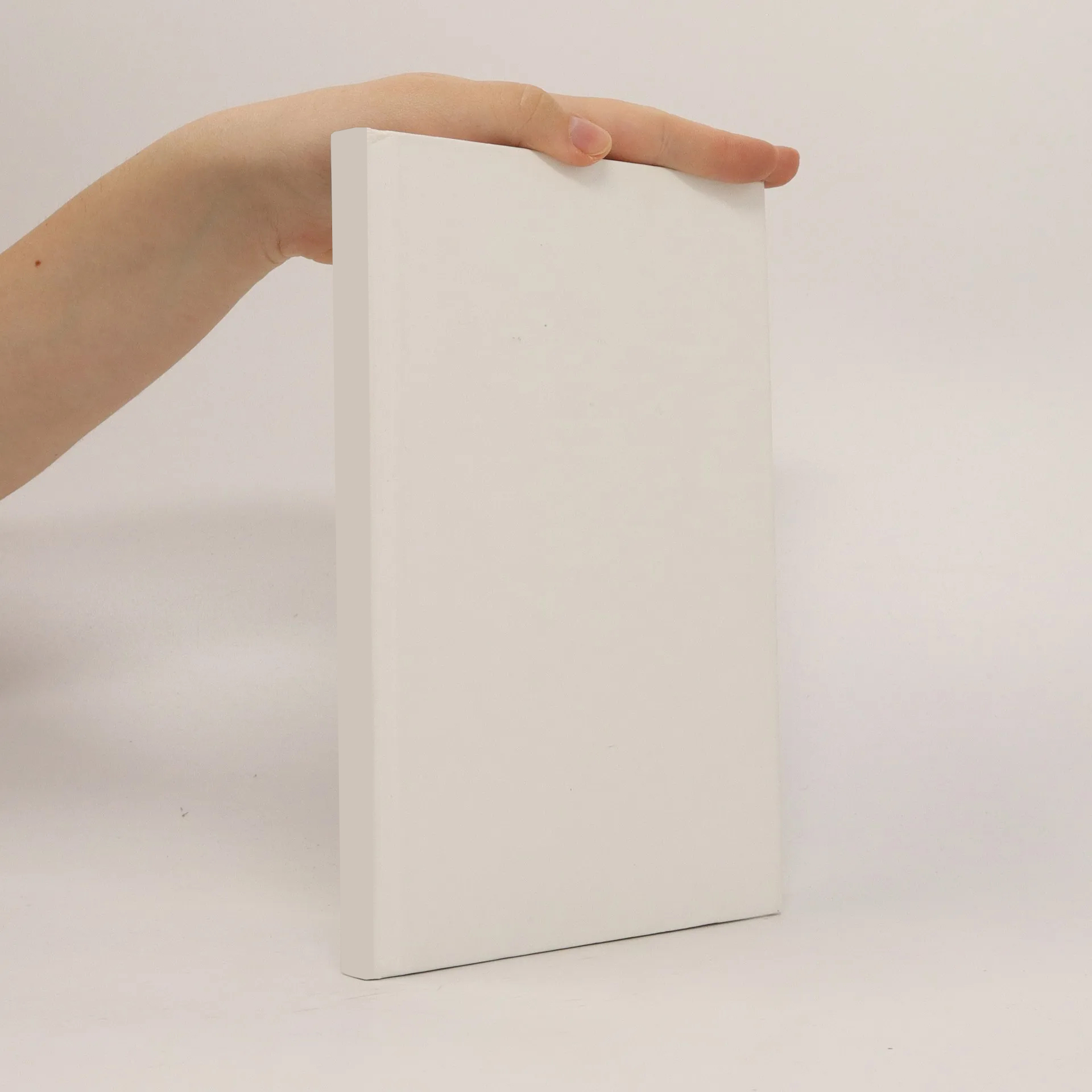
Parametry
Více o knize
Beginning with a short introduction of the basics of active magnetic bearing system, the existing self-sensing techniques are explained. Over these different approaches, the current slope based technique is chosen as the object for the research and optimization due to its advantages in modeling and implementation. The industrial magnetic bearings are mostly driven by PWM (Pulse Width Modulation) amplifiers. This results in the unavoidable current ripple due to the voltage switching. The positive or negative slope of the current ripple contains the position information of the levitated bearing object of the magnetic bearing. As a preliminary research, a single current slope based approach was completed, which only considers the positive current slope. The approach includes the deduction of the algorithm for the position estimation, the construction of a prototype and the experimental validation. The concept of multiple current sampling is validated. Instead of measuring with a transformer, the current slope of one PWM switching state is calculated, using the method of least squares from multiple samples of the current. For the levitation control with estimated position, this concept achieves the minimum amount of hardware, which is as simple as that for a pure current control. The modeling with single current slope shows limited ability to exclude the affects due to the coil resistance and the induced voltage, which is caused by the movement of the rotor. Therefore, the double current slope based modeling is introduced, which considers both the positive and negative slopes of the current ripple, and eliminates the above mentioned affects significantly. Furthermore, one PWM period is split into two sub-cycles — the sensing cycle and the control cycle. This reduces the amplitude of the current ripple to its halve, while maintains the accuracy of the position estimation. One issue of the existing self-sensing approaches is the doubled number of power amplifiers than conventional AMBs, because they all apply the classical differential driving mode to obtain two independent currents per axis of motion. This is mandatory for the position estimation. On the other hand, the conventional AMBs can use the differential winding, which only needs one power amplifier per axis of motion. The author proposes a new coil configuration — the parallel differential winding, which uses the same number of power amplifiers as conventional AMBs, but can still perform the proposed double current slope based position estimation. A second prototype was built to validate the above mentioned improved self-sensing technique, and an industrial homo-polar radial magnetic bearing with PM (Permanent Magnet) excited bias fluxes was driven with the estimated position. The experimental results show very good performance of the self-sensing levitation control. The proposed position estimation technique is proven to be accurate, dynamic and true cost saving. Self-sensing magnetic bearings with this technique can be considered as a potential competition against the conventional AMBs in the field of vacuum pumps, flywheels and high speed blowers, where extremely accurate position control is not required.
Nákup knihy
The current slope based position estimation for self-sensing magnetic bearings, Jinou Wang
- Jazyk
- Rok vydání
- 2016
Doručení
Platební metody
Navrhnout úpravu
- Titul
- The current slope based position estimation for self-sensing magnetic bearings
- Jazyk
- anglicky
- Autoři
- Jinou Wang
- Vydavatel
- Shaker Verlag
- Rok vydání
- 2016
- ISBN10
- 3844044868
- ISBN13
- 9783844044867
- Kategorie
- Skripta a vysokoškolské učebnice
- Anotace
- Beginning with a short introduction of the basics of active magnetic bearing system, the existing self-sensing techniques are explained. Over these different approaches, the current slope based technique is chosen as the object for the research and optimization due to its advantages in modeling and implementation. The industrial magnetic bearings are mostly driven by PWM (Pulse Width Modulation) amplifiers. This results in the unavoidable current ripple due to the voltage switching. The positive or negative slope of the current ripple contains the position information of the levitated bearing object of the magnetic bearing. As a preliminary research, a single current slope based approach was completed, which only considers the positive current slope. The approach includes the deduction of the algorithm for the position estimation, the construction of a prototype and the experimental validation. The concept of multiple current sampling is validated. Instead of measuring with a transformer, the current slope of one PWM switching state is calculated, using the method of least squares from multiple samples of the current. For the levitation control with estimated position, this concept achieves the minimum amount of hardware, which is as simple as that for a pure current control. The modeling with single current slope shows limited ability to exclude the affects due to the coil resistance and the induced voltage, which is caused by the movement of the rotor. Therefore, the double current slope based modeling is introduced, which considers both the positive and negative slopes of the current ripple, and eliminates the above mentioned affects significantly. Furthermore, one PWM period is split into two sub-cycles — the sensing cycle and the control cycle. This reduces the amplitude of the current ripple to its halve, while maintains the accuracy of the position estimation. One issue of the existing self-sensing approaches is the doubled number of power amplifiers than conventional AMBs, because they all apply the classical differential driving mode to obtain two independent currents per axis of motion. This is mandatory for the position estimation. On the other hand, the conventional AMBs can use the differential winding, which only needs one power amplifier per axis of motion. The author proposes a new coil configuration — the parallel differential winding, which uses the same number of power amplifiers as conventional AMBs, but can still perform the proposed double current slope based position estimation. A second prototype was built to validate the above mentioned improved self-sensing technique, and an industrial homo-polar radial magnetic bearing with PM (Permanent Magnet) excited bias fluxes was driven with the estimated position. The experimental results show very good performance of the self-sensing levitation control. The proposed position estimation technique is proven to be accurate, dynamic and true cost saving. Self-sensing magnetic bearings with this technique can be considered as a potential competition against the conventional AMBs in the field of vacuum pumps, flywheels and high speed blowers, where extremely accurate position control is not required.